"Perito" argumentando que via seca é de segunda linha porque queima menos que via úmida. Também disse que via seca é feita de argila, barro. E que via seca é mais porosa...
Recuperado e vivo, após ouvir tais argumentações, explico:
👉 Cerca de 80% de tudo que é fabricado em via seca ou via úmida no Brasil é do grupo de absorção BIIb que tem porosidade entre 6 e 10%;
👉 É o grupo de absorção que permite a maior aderência da argamassa porque "absorve" a água, o cimento e os aditivos da argamassa e assim a chance de descolamento é menor;
👉 Ocorrem mais casos de descolamento no grupo BIIb simplesmente porque a produção é muito maior se comparada à via úmida (também falamos sobre isso aqui). Produz mais, usa mais, podem ocorrer mais casos quando o assentamento é malfeito e com argamassa inadequada;
👉 Via seca não é feita de barro ou de argila comum como tijolo, por exemplo. Tudo fica vermelho quando queima tijolo ou nossas cerâmicas porque aqui existe o corante natural "óxido de ferro".
O polo cerâmico de Santa Gertrudes nasceu e cresceu sobre um grande "depósito" de matérias primas para fabricação de cerâmicas via seca.

A área denominada Formação Corumbataí se destaca do resto do Brasil pela grande quantidade de feldspato sódico mineral que age como poderoso fundente durante a queima de nossos revestimentos cerâmicos.
Uma montanha de pedra que precisa ser dinamitada. Um verdadeiro "sanduíche" de rochas e outros minerais depositados em camadas durante os diversos períodos da formação da Terra.

As matérias primas são retiradas e misturadas antes de serem moídas sem água, em seguida recebem um pouquinho de água para formar uma "massa" com 10% de umidade e permitir a prensagem no formato inicial da cerâmica.
A mistura das matérias primas tem cor clara antes da queima e se tornam avermelhadas após a queima coloridas pelo óxido de ferro que faz parte da sua composição.

Veja como a placa "encolheu" após a queima.
Durante a queima entra em ação o fundente feldspato que promove a sintonização (entenda com greseificação) de onde vem o termo grés.
O feldspato funciona como uma "cola" unindo o pó de todas as matérias primas e as transformando novamente em uma pedra cerâmica na forma de uma cerâmica.
Daí o "perito" diz que são cerâmicas mal queimadas, blá-blá-blá... Vejam o tamanho de nossos fornos:
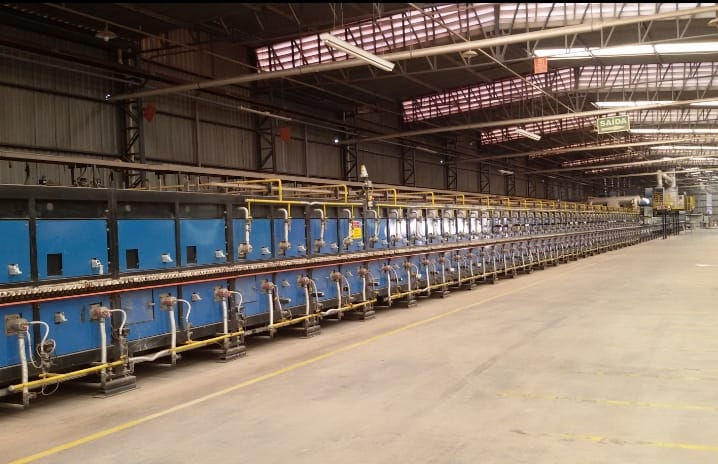
Tudo fica incandescente à 1.200 graus. Temperatura que nem o aço resiste.
Não satisfeito, o "perito" argumenta que o tal pozinho branco no verso da cerâmica impede a aderência da argamassa. O tal pó é caulim, o mesmo que está presente em todas as argamassas colantes, no contrapiso, no reboco, no concreto...